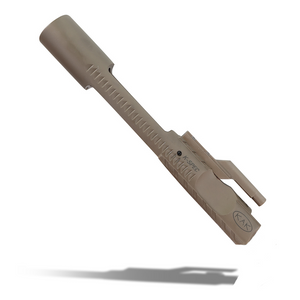
Slotted Angled Carrier Rails
For enhanced functionality in adverse and rugged conditions such as sand, mud, dirt, and grime. These rail cuts are designed for debris disbursement, resulting in ultra-high functionality in the toughest conditions, including suppressor fouling and foreign contaminates. Strategically located angle cuts in the rails result in fouling and debris being moved into noncritical areas that are not in contact with the receiver and do not affect the function of the firearm. aka sandcutter
- Designed to function reliably in the toughest conditions
- Angled Carrier Rail Cuts for flawless function in adverse conditions and prolonged suppressed use
- Full Auto Profile
- Permatex added between Gas Key and Carrier Mating Surface
- Carrier- 8620 steel, outside rails, bolt runs, and gas bores ground to .0002 tolerances, FDE PVD Finish
- Gas key – 4130 steel, heat treated, secured with T25 torx fasteners, torqued to spec, staked with hydraulic staking machine
- 9.5 oz
Machined in house and assembled using only the finest steels and components.
KAK Industry takes pride in producing some of the finest Mil-Spec/ Enhanced AR15 bolt carrier groups available, made 100% in house at our MO facility using Doosan machining centers, Tsugami Swiss turning, and the latest in FANUC robotics combined into an automated cell giving us lights out production capability. In house automated CMM Inspection processes ensure consistent quality.
PVD (Physical Vapor Deposition) coating is a process used to apply thin films or coatings to surfaces, offering a range of benefits depending on the material and application. PVD is widely used in various industries, including aerospace, firearms, and manufacturing, due to its ability to improve surface properties such as hardness, corrosion resistance, and aesthetic appearance.
How PVD Works
- Vaporization: A material (typically a metal or metal compound) is vaporized in a vacuum chamber. This can be done using techniques like sputtering or evaporation.
- Deposition: The vaporized material then condenses onto the substrate (the surface being coated) to form a thin, solid film.
- Bonding: The coating adheres to the substrate surface, forming a durable layer.
Benefits of PVD Coatings
- Durability: PVD coatings are known for their hardness and wear resistance, which makes them ideal for applications where surfaces are subject to friction or abrasion.
- Corrosion Resistance: They provide excellent protection against corrosion, extending the lifespan of the coated materials.
- Finish:
- FDE PVD
- Type:
- K-SPEC ENHANCED
- Hand Preference:
- Right Hand